PLC(Programmable Logic Controller,可编程逻辑控制器)作为工业自动化领域的核心控制元件,正引领着机器人控制技术迈向新的高度。其强大的数据处理能力、灵活的编程接口以及高可靠性的运行特性,使得PLC成为控制机器人执行复杂、精确任务的选择方案。
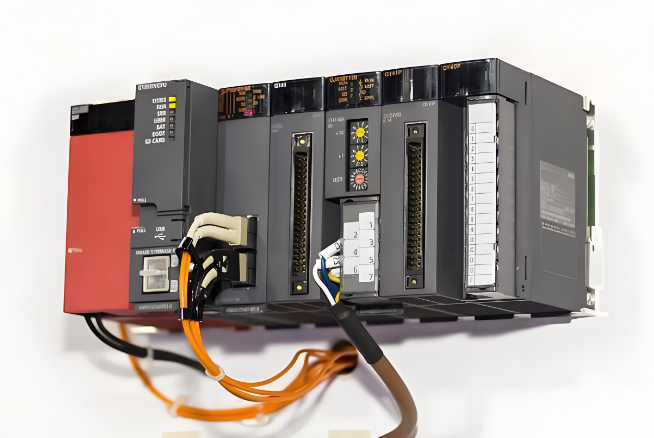
一、PLC在机器人控制中的应用原理
PLC是一种专为工业环境设计的数字运算操作电子系统,它采用可编程的存储器,用来在其内部存储执行逻辑运算、顺序控制、定时、计数和算术运算等操作的指令,并通过数字或模拟的输入/输出控制各种类型的机械设备或生产过程。在机器人控制中,PLC通过接收来自机器人传感器的输入信号,根据预设的程序进行逻辑运算和判断,然后输出控制信号给机器人的执行机构,实现对机器人的精确控制。
二、PLC控制机器人的步骤
1、明确控制需求:首先,需要明确机器人的控制需求,包括机器人的运动轨迹、速度、加速度、定位精度等。这些需求将直接影响PLC程序的编写和配置。
2、选择合适的PLC型号:根据机器人的控制需求,选择合适的PLC型号。在选择时,需要考虑PLC的处理能力、输入/输出点数、通信接口等因素,以确保PLC能够满足机器人的控制需求。
3、编写控制程序:使用PLC的编程语言(如梯形图、指令表等)编写控制程序。在编写程序时,需要充分利用PLC的逻辑运算、顺序控制、定时计数等功能,实现对机器人的精确控制。
4、连接输入输出接口:将PLC的输入输出接口与机器人的传感器和执行机构进行连接。在连接时,需要注意信号的匹配和转换,以确保PLC能够正确接收和发送信号。
5、测试和调试:在PLC程序编写和配置完成后,需要进行测试和调试。通过模拟机器人的实际工作环境和条件,测试PLC程序的正确性和可靠性,并进行必要的调整和优化。
三、PLC控制机器人的应用场景
PLC控制器在工业机器人控制系统中有广泛的应用场景,包括但不限于以下几个方面:
1、装配/焊接作业:PLC可通过专用的运动控制模块,精确控制机器人各关节的位置、速度和力矩,实现复杂的动作编程,广泛应用于汽车制造、家电生产等行业的零件装配和焊接作业。
2、、表面处理:在喷涂、抛光等表面处理工序中,PLC控制器可准确控制机器人的动作轨迹和速度,确保涂层均匀一致,并监测涂料喷涂量、喷涂压力等关键参数,及时进行工艺调整。
3、物料搬运:利用PLC可编程的逻辑控制功能,可以实现对机器人抓取、搬运、码垛等动作的精准控制,提高生产效率,减少人工操作的安全隐患,广泛应用于仓储物流、码头装卸等场景。
4、质量检测:PLC可通过输入输出接口,配合视觉系统、力矩传感器等,精确控制机器人完成产品的自动化装配和质量检测,提高检测效率和准确性。
5、危险环境作业:在一些高温、辐射、爆炸等危险作业环境中,PLC控制的工业机器人可代替人工完成作业,大大提高作业安全性,如核电站内部检修、化工厂危险区域作业等。
四、PLC控制机器人的优势
1、高可靠性:PLC采用的硬件和软件系统非常稳定可靠,工作周期长,适用于工业自动化的各种环境和场合。
2、灵活性高:PLC的输入和输出接口可根据需要进行扩展,可适用于各种工业自动化领域。
3、易于编程:PLC的编程语言通常是基于国际通用标准IEC61131的,简单易学,便于掌握。
4、编辑、调试和维护方便:PLC的程序编辑和调试通常以图形化方式进行,操作简单,维护方便。
随着PLC控制技术的不断演进与机器人技术的飞速发展,两者之间的融合日益紧密,共同绘制出工业自动化领域的新蓝图。PLC作为机器人控制系统的核心驱动力,不仅极大地提升了机器人的智能化水平和作业效率,还为企业带来了更高的生产灵活性、更低的运营成本以及更显著的安全性能。